About Holz-Wastl
Company and philosophy
History
From family business to global corporation
It is due to pure coincidence in 1984 - a conversation with an acquaintance - that Holz Wastl entered the automotive industry.
Driven by the necessity to acquire an additional supplier for shelving boards, Holz-Wastl was very promptly incorporated into the supplier portfolio of a 1st tier, which is still located in Austria.
This was convenient for Holz-Wastl, as the core business with timber trade had stagnated following the opening of the East.
Back then, as is the case today, solid and high-quality work was absolutely in focus. Thus, following an initial shelving board, another order came through, and the entry into the automotive supplier business was established.
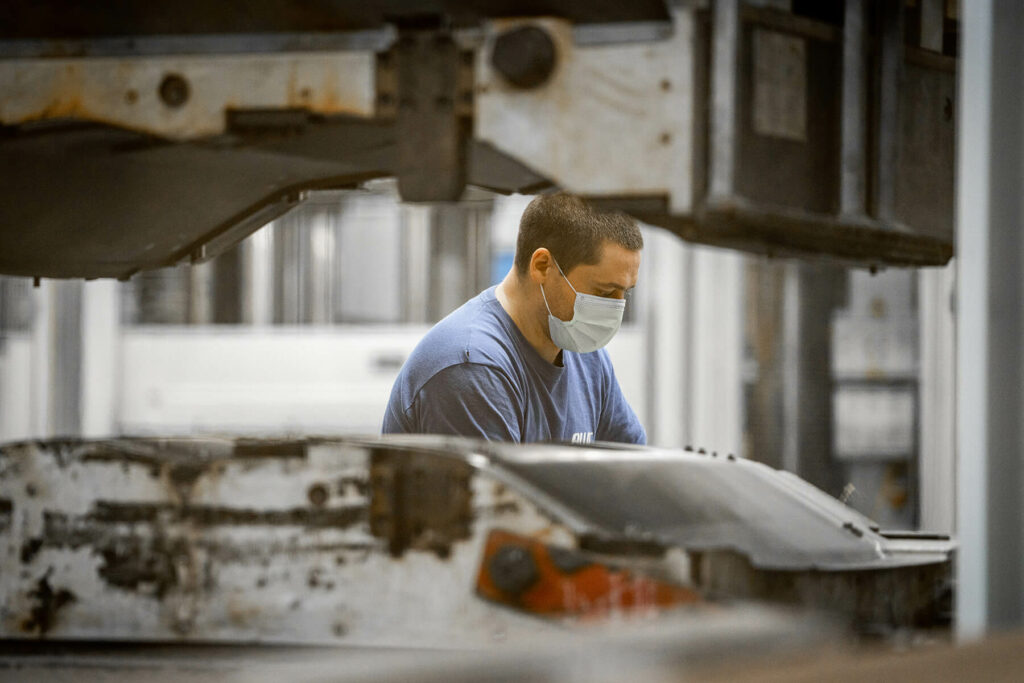
The portfolio was expanded and soon included the complete production of complex components and panels. Various laminated components such as parcel shelves, covers from our own PU production and from 2020 even columns from the back injection process that was also installed were added.
The passion for exclusive cars and their equipment, which the founders, Hans-Peter Fennes and Herbert Wastl-Fennes, had from an early age, grew steadily, as did the company. Parts from the Holz-Wastl production facilities are installed in numerous vehicles in the high-end category.
In 2021, the management was handed over to the next generation, Ulrike and Philip. Along with the business responsibilities, they also passed on their love for beautiful cars to them.
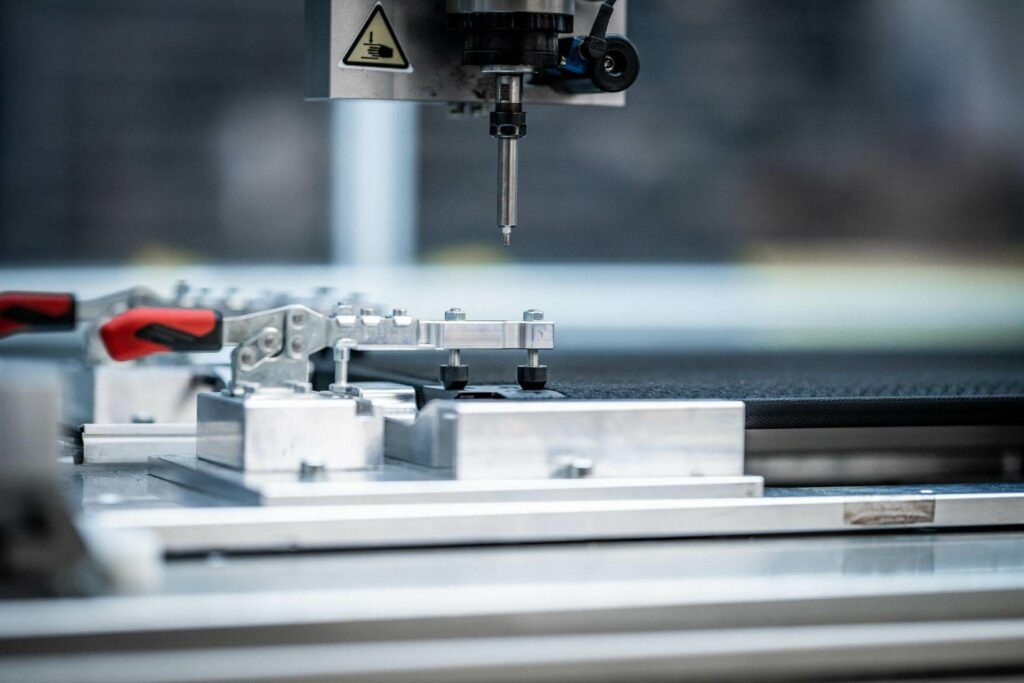
For over 35 years Holz Wastl has been one of the absolute experts in the automotive supply industry.
The healthy, thriving family business, which now has an average of about 800 employees, relies on steady, honest, and dependable business relationships.
Nowadays, Holz-Wastl is considered a specialist in interior fittings within the industry. The long-standing expertise in this field is internationally appreciated and recognized. Strategic partnerships and networking ensure reliability and the highest level of professionalism.
Holz-Wastl today
Strategic partner with expertise and experience
Procurement
Holz Wastl sees itself as a contemporary, constantly growing company certified according to IATF 16949, ISO 14001 and ISO 45001.
Bringing innovative, valuable products with the highest quality standards to the customer on time is the focus of our work.
Functioning partnerships and long-standing business relationships confirm our constant and reliable work.
Our procurement therefore continues to invest in the selection and qualification of partners. New processes for this have already been installed and will
constantly implemented.
Locations
Strong partners who trust in us
In Eisenstadt – the company headquarters – you can find the executive management, sales, purchasing, development, and also the logistics department.
General customer support is centrally located in Eisenstadt. Within our own plant construction, prototype development and spare parts management are situated.
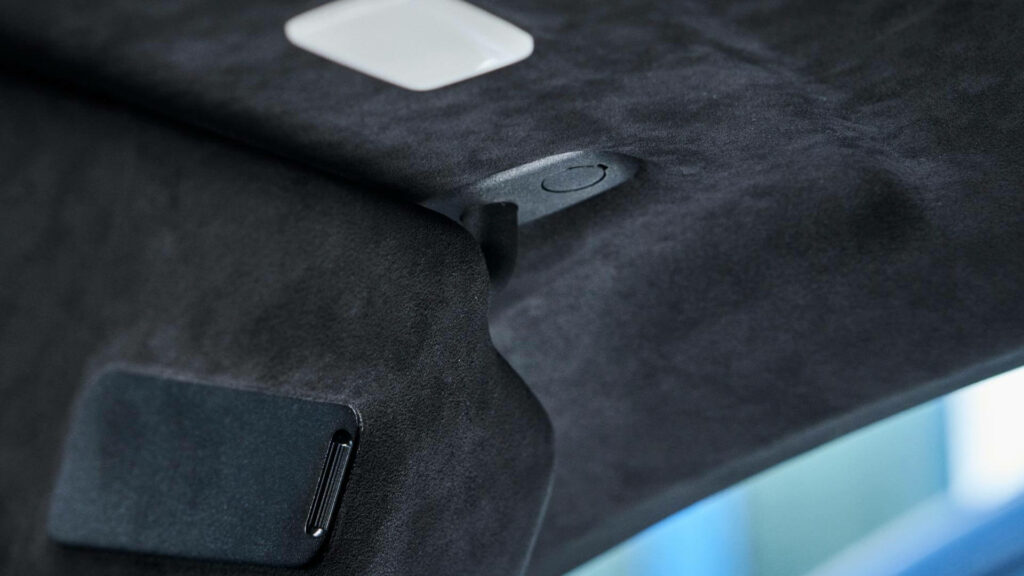
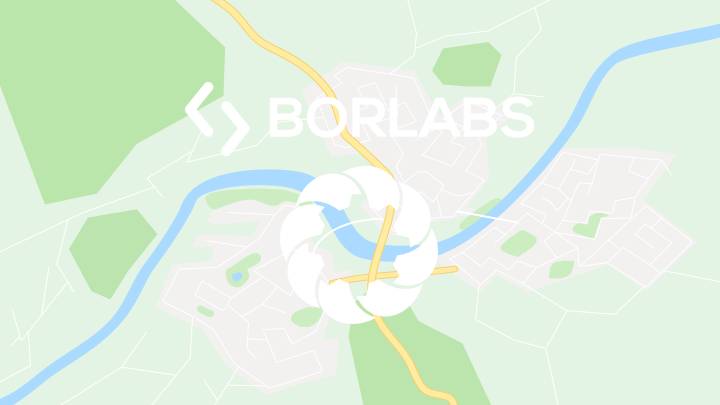
By loading the map, you accept Google's privacy policy.
Learn more
In Sopron the factory halls "Autoteile Wastl Fennes" - AWF 2 to 4 are located.
While at AWF 2, the focus is on column claddings (finishing and Just-In-Sequence sequencing), headliner production (small roof coupés and roadsters), lamination, covers from our own sewing department and finishing (PU semi-rigid foam systems), as well as small series productions, AWF 3 manufactures parcel shelves, self-supporting PU systems, upper and lower column claddings including lamination, trunk areas (including PU honeycomb systems, lamination, finishing, and assembly), trunk side claddings (finishing – assembly), door panel components, armrests, door sills, side panels, back-foamed PU soft foam systems complete with lamination and finishing.
At AWF 4, we manufacture headliner coverings with PU semi-rigid foam systems, supports for both large and small roofs with lamination that is either semi- or fully-automatic, as well as semi- or fully-automatic finishing and Just-In-Sequence (JIS) sequencing.
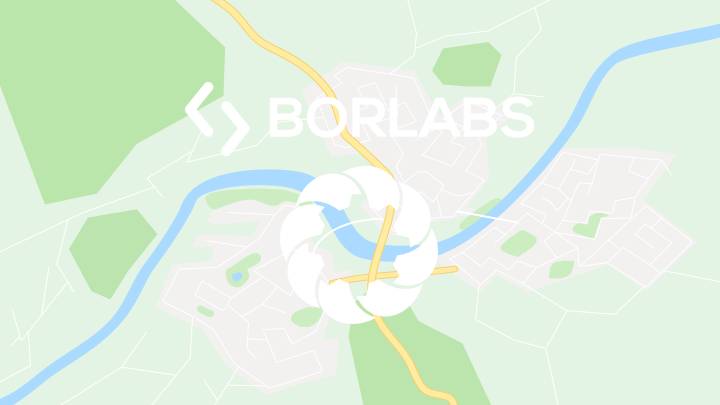
By loading the map, you accept Google's privacy policy.
Learn more
In Sarvar, we produce parcel shelves, shelf inserts, and column claddings.
Press lamination, honeycomb panel production, back-injection molding, and thermoforming are among our core competencies there.
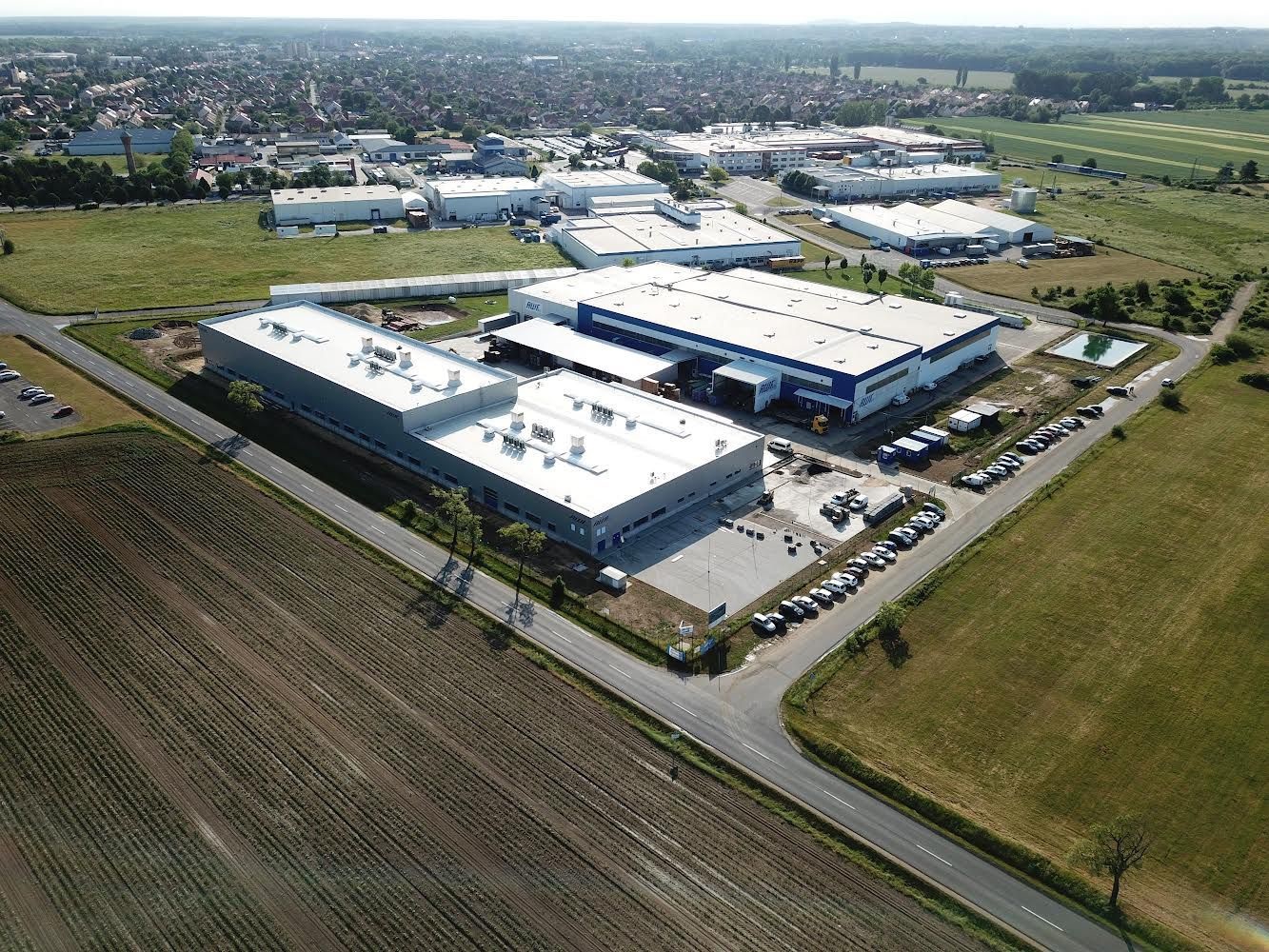
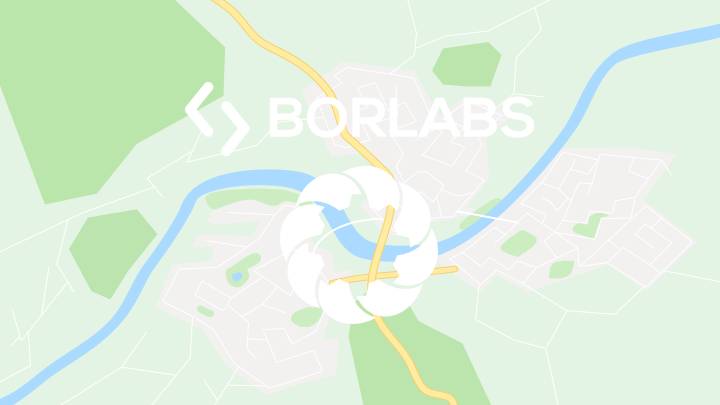
By loading the map, you accept Google's privacy policy.
Learn more
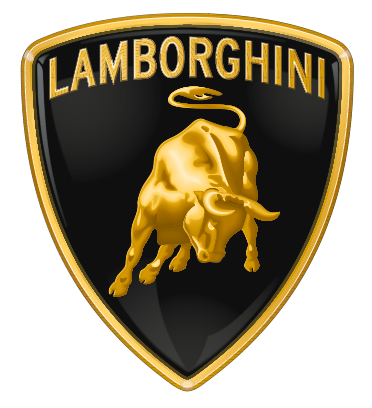
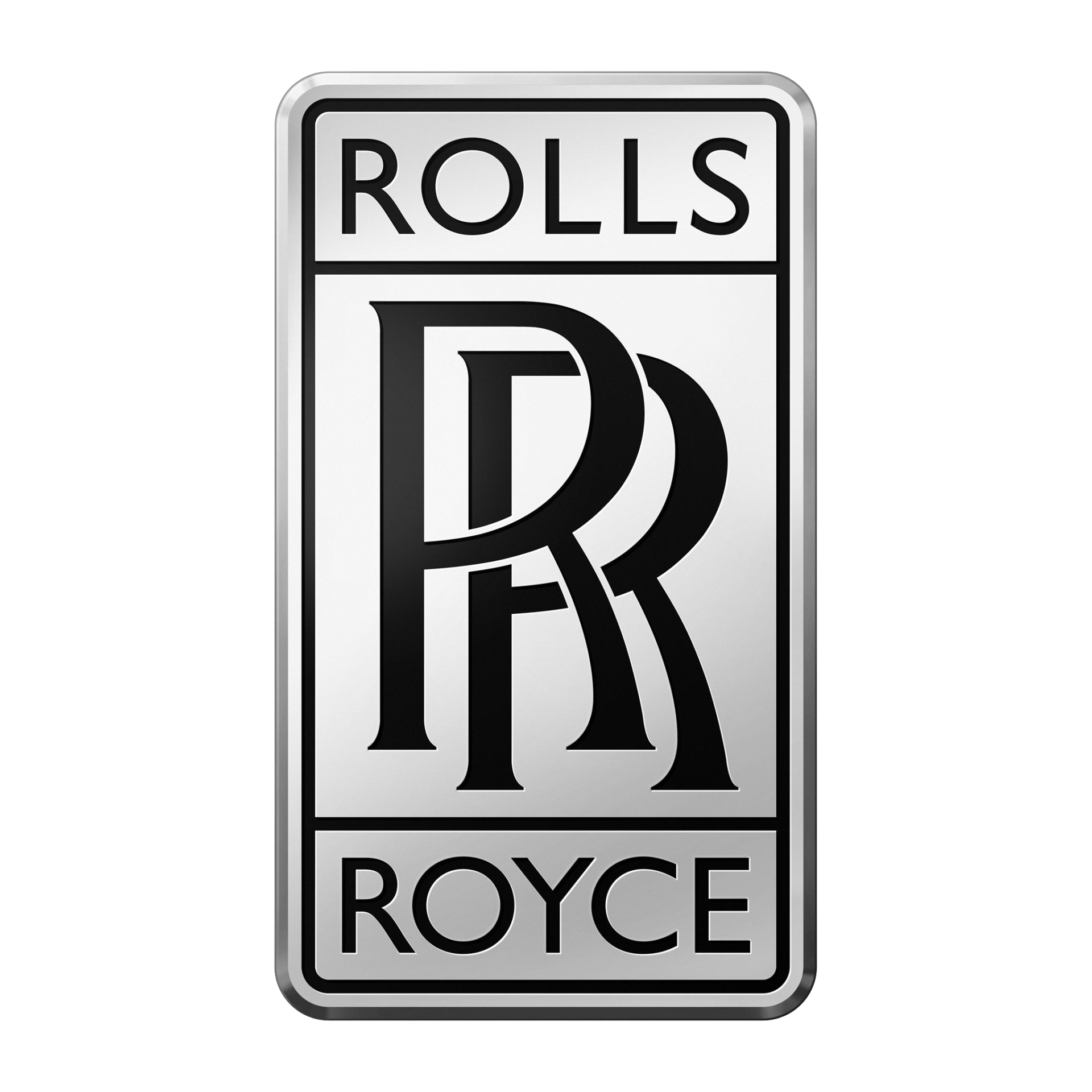
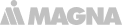
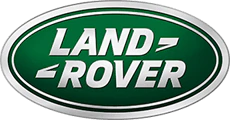
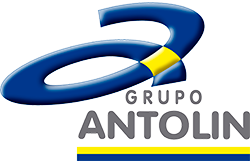